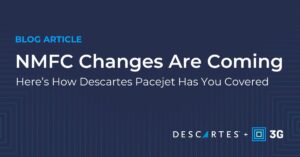
NMFC Changes Are Coming — Here’s How Descartes Pacejet Has You Covered
Big changes are coming to freight classification standards this summer — and Descartes Pacejet is already preparing so you don’t have to worry. Effective July
Move everything over the road more optimally with the industry’s most powerful planning algorithm
Most complete and connected over-the-road network for LTL, parcel, 3PL, Truckload carriers
Best-in-class packing and shipping for faster fulfillment with fewer errors and less labor
Integration software that quickly connects your business to customers, carriers, partners
Pre-integrated access to ERP and financial applications like NetSuite, Acumatica, or IFS
Pre-integrated access to popular applications, industry specialists, and value-add services
Unlock expert tips and cutting-edge strategies that help shippers, 3PLs, and brokers streamline logistics, reduce costs, and stay ahead in a dynamic logistics industry
Discover real-world success stories where innovative leaders have revolutionized their logistics with 3G’s powerful solutions
Get the latest updates and breakthroughs from 3G, and see how we’re driving the future of shipping and transportation management
Connect with industry experts and peers at events, where you’ll gain the knowledge and insights needed to lead in logistics
Big changes are coming to freight classification standards this summer — and Descartes Pacejet is already preparing so you don’t have to worry. Effective July
More Power in Self-Service Shipping Paperwork Self-service shipping paperwork gives Descartes Pacejet users the flexibility to configure, update, and manage packing slips, labels, and other
Leveraging TMS and Shipping Software to Automate Freight Classification Determining the correct freight class is crucial for optimizing shipping costs and ensuring smooth logistics operations.
Unlocking Cost Savings and Operational Efficiency Through ERP Integration Managing shipping and logistics can be complex and costly but integrating shipping software with your Enterprise
Introducing the 4-Part Series on Scanning for Shipping Efficiency Shipping errors can lead to lost revenue, dissatisfied customers, and costly returns. Manual data entry is
Over half of online consumers aged 18-34 expect same-day delivery, and 61% are willing to pay more for it. While “same-day delivery” isn’t the same
Learn how automation in transportation management can help shippers overcome the skills gap and improve efficiency.
If you’ve been relying on parcel shipping to meet your business’s needs, you may have noticed that as volumes grow or shipments get larger, parcel
In today’s dynamic shipping landscape, staying ahead of changes and continuously enhancing carrier network integrations is crucial to delivering a seamless shipping experience. At 3G,
A lot of shippers start thinking about return logistics around the beginning of the year: The holidays have just ended, a new year is starting,