Blog
How a TMS Creates Freight Management Efficiencies
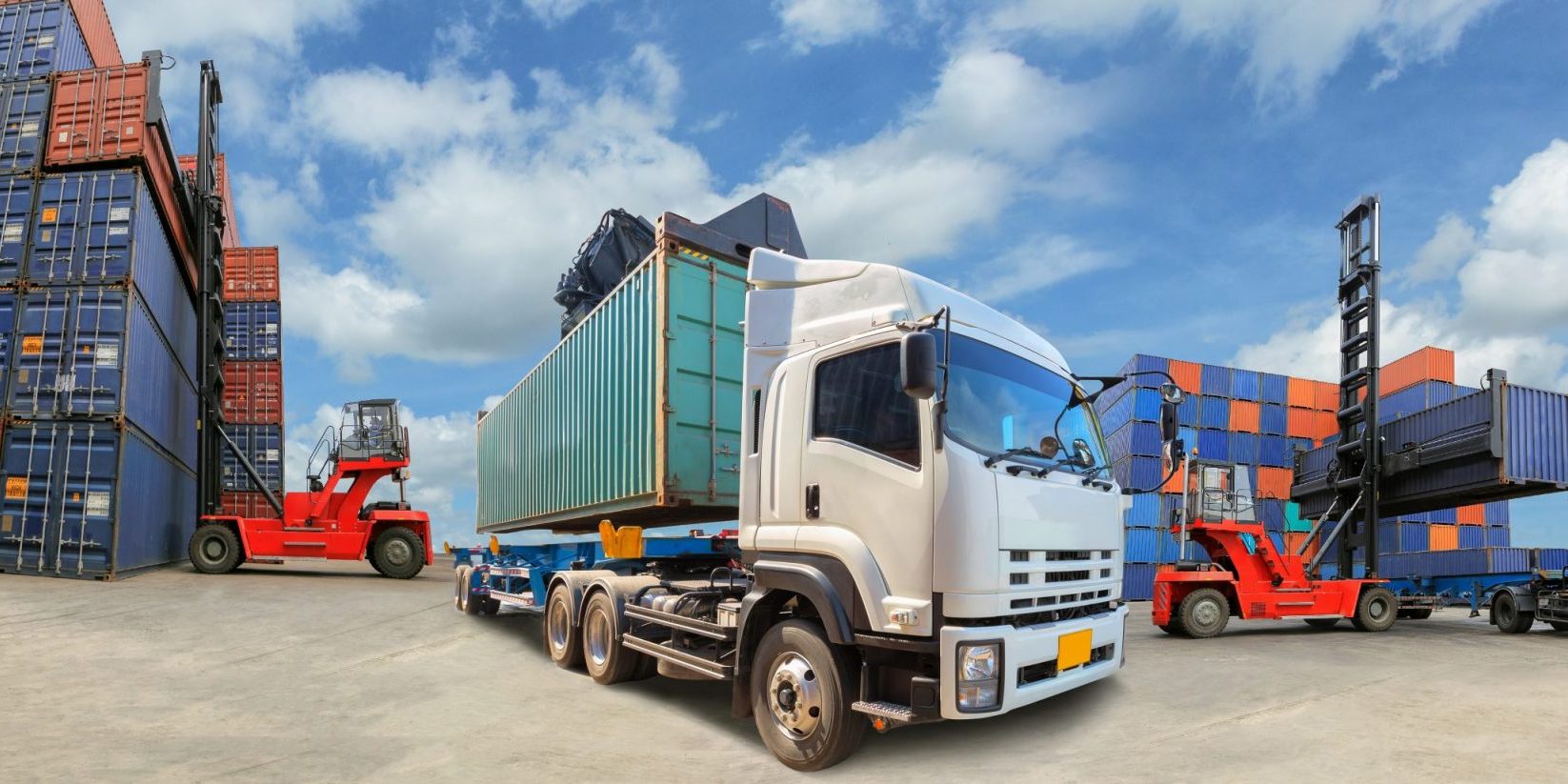
Today’s supply chain moves a lot of freight.
In 2018, the US alone transported around 51 million tons of freight daily valued at over $51.8 billion, according to the US Department of Transportation’s (DOT) Bureau of Transportation Statistics (BTS). Calculations of DOT data by Freight Analysis Framework estimate the amount of freight to increase about 1.2% yearly between 2018 and 2045.
What’s more is the substantial impact of freight shipments on the economy. In 2019, transportation contributed an estimated total of $1.3 trillion to the US GDP, with trucking contributing $368.9 billion of that total. Now, in 2022, these numbers continue to grow despite the world facing supply chain challenges.
To keep up with the immense volume and increasing demand for freight shipments, freight management companies demand greater efficiencies. By turning to a technology solution like a cloud-based transportation management system (TMS), brokers, shippers, and 3PLs can handle the greater complexities of freight management today. Learn how in this post. And see how using a TMS helps freight management companies increase efficiency and improve service, while saving time and money.
Freight management challenges that demand change
Apart from today’s supply chain challenges, transportation companies also face the following freight management challenges:
- Documentation: Freight management requires high volumes of documentation—from dispatch notes and invoicing to certificates of compliance and clearances. Managing these documents requires effective and accurate record-keeping, which isn’t possible with time-consuming and error-prone traditional manual processes.
Automating document handling with a TMS, using exception-based management, dramatically reduces processing time and eliminates data entry and re-entry errors.
- Order fulfillment scheduling: Operationally, scheduling order fulfillment is a major daily challenge for freight management, especially when doing it manually.
Automating scheduling with a TMS turns a multi-part puzzle into an algorithmically optimized process that improves customer service and uncovers cost savings.
- Order and route tracking through delivery: Tracking routes and orders through delivery is nearly impossible to do manually.
Today’s TMS technology automates tracking, providing real-time visibility into fulfillment. It also sends alerts about any issues or problems to resolve and includes critical order and delivery information customers expect.
How a TMS creates freight management efficiencies
A TMS offers shippers, brokers, and 3PLs multiple benefits, including visibility across the fulfillment process and management of day-to-day functions in a centralized platform. Through portals, customers and carriers connect with TMS users, creating an integrated ecosystem that streamlines customer service and maximizes costs and time savings. Beyond these advantages, discover three ways a TMS creates freight management efficiencies.
Optimization through data, algorithms, and analytics
Data from internal and external sources fuels optimization algorithms and performance analytics and reporting in a TMS. The external data comes from systems like inventory databases, vendor databases, and fulfillment systems. The internal organizational data, such as carrier performance and customer service metrics, combines with the external supply chain data sources to automate and improve freight management functions.
Consolidate the internal and external data that powers algorithms, analytics, and reporting to automate and optimize key functions across the freight management process to save time and money.
In a TMS, efficiency begins at the highest level by consolidating data, analytics, and reporting on one platform. Instead of relying on multiple technology solutions, shippers, brokers, and 3PLs use a TMS to build a single data repository from the following sources, among others:
- Order management
- Route optimization
- Enterprise resource planning (ERP) systems
- Internet of things (IoT) sensors and tracking devices
- Real-time pricing updates
- Government-provided transportation industry data
With this data in one place, the TMS optimizes freight management functions, such as order, route, and load management. Even greater value comes with incremental improvements across the entire freight management process. When combined, they add up to significant savings in time and cost.
While incremental improvements might seem small, they have a major impact. For example, a TMS automates spot quoting by examining historical lane pricing data and evaluating current market rates across supply chain partners. Imagine applying this type of optimization to every freight management function.
End-to-end automation
Automation becomes a reality for freight management companies with centralized data repository, algorithms, analytics, and reporting. A TMS automates tasks and functions that are traditionally handled manually, enabling exception-based management. For example, you can configure a TMS with rules to flag freight bills that fall outside established thresholds as exceptions for rejection or further investigation.
Automate across operations from carrier, route, and load management to freight audits and payment with a TMS for a fulfillment-wide process that enables exception-based management.
The efficiencies created by data and automation work hand in hand. Without data, automation isn’t possible, and if data and analytics aren’t used to automate operations, you’re not tapping into its full value.
By using a TMS, shippers, brokers, and 3PLs improve carrier management in the following ways:
- Automate carrier qualification, onboarding, contract management, and carrier assignment, among other tasks.
- Quickly post to load boards when pricing loads.
- Review historical lane pricing and evaluate current market rate conditions based on system integration with supply chain industry partners.
- See and analyze performance data based on analytics and reporting to choose the right carrier for each job.
For route and load management, a TMS provides the ability to:
- Gain visibility into truck routes through automated fleet tracking, helping to optimize and consolidate routes and loads.
- Improve fleet efficiency with route performance monitoring based on analytics.
- Use algorithms to automatically recommend carriers for orders based on criteria like shipment size, location, and delivery requirements.
A TMS also automates freight audits and payments, saving time and money by enabling a process that:
- Tracks invoice details.
- Finds duplicate billing.
- Ensures the receipt of accessorial services with discounts applied.
Improved customer service
Great customer service is an organizational goal to retain valuable customers and provide as a selling point for new customers. But it’s a challenge in today’s complex supply chain. Not with a TMS. It gives shippers, brokers, and 3PLs tools that meet expectations of the modern logistics customer. A TMS delivers customer service by providing efficiencies to automate freight management functions and tap into the power of big data and analytics.
Improve your customer service by automatically uncovering fulfillment issues, providing the tools necessary to fix problems, and communicating with customers across the entire delivery process.
TMS-powered visibility into the supply chain means customers get real-time alerts on deliveries and delays. When the TMS uncovers delivery problems, it alerts customer service agents and provides the relevant order information to resolve the situation. It streamlines the process by suggesting solutions.
The TMS optimizes the order-to-delivery cycle by providing better service in daily operations. It also gives tools and data to supply chain providers so they can help their customers make better business decisions. These providers can share performance metric data with customers, giving them information to improve their own analytics. Such data includes:
- Shipping costs
- Time of transit
- On-time delivery rates
- Damage rates
To understand how a TMS improves customer service, consider the example of managing a routing issue. Because the TMS provides visibility into an order, when it identifies a problem, the following events occur:
- The TMS creates an automated alert about the problem.
- A customer service agent notifies the customer about a potential delay.
- Freight managers and customer service representatives receive information from the TMS about the problem.
- The TMS prompts the freight management team on how to solve the problem.
- The customer service agent reassures the customer that the situation is under control.
After the team solves the problem, the customer receives their order—satisfied and with new confidence and trust in the freight management provider.
Transform your freight management operations
For supply chain providers, freight management is central to profit and loss. TMS freight management efficiencies add up to significant time and operational cost savings—5% – 15% on average with a productivity gain of 5% – 10% according to Gartner.
For shippers, brokers, and 3PLs, a TMS delivers a configurable, multimodal, cloud-based solution. It’s flexible enough to meet any transportation lifecycle challenge and ready to scale and grow with any business.
Learn more about how a TMS can make your supply chain more efficient. Download the datasheet: A TMS Designed for You.