Blog
Why Shipping Piece Count Errors Occur and How to Prevent Them
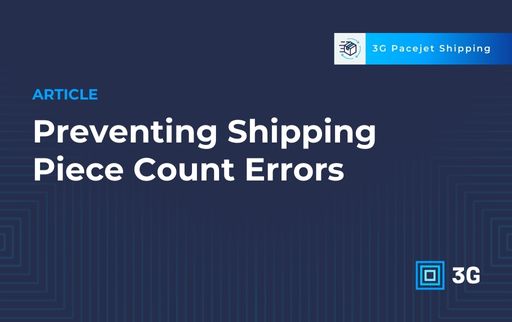
Piece counts are the type of shipment detail that seem straightforward but can easily lead to errors without the right workflow in place. In fact, piece count is on the list of the most common shipping errors, which can be identified by a shipping audit. Unlike others on the list, piece count doesn’t require special knowledge to get correct, and fixing these errors can save your shipping operations money as well as time.
What causes piece count errors
It might seem like piece count discrepancies are simply one-off mistakes, caused by human error, but they actually indicate a different problem, one of the processes and technology used by warehouse staff. Employees should be able to rely on technology for the packing workflows so that there is no chance of handling piece count, or any other detail of shipment information, 100% manually. Even technology-assisted counting shouldn’t have any redundant processes like retyping the information that could lead to keystroke errors.
The workflow of preparing a shipment should merge the manual work required with technology—by scanning items as they are added to the pallet, crate, or other container. This way, the items are recorded the moment they are packed, and the program takes care of the counting.
Piece count errors are more likely to show up in one of the following shipping situations.
Multi-package shipments
For non-palletized freight, multi-package shipments are an opportunity to save on shipping costs, but there’s also the potential for a disconnect between entering in information like the piece count and creating the shipment. When recording the piece count is a separate process as without automation, this is where errors are likely to occur.
Consolidating
If there are multiple orders going to one destination, you may decide to consolidate these shipments to pallets or crates to save money. It’s important to have a system to handle consolidation accurately and without any manual processes of typing in information. Without technology taking care of this, it would be easy to make a mistake on the new piece count.
What happens when a piece count error occurs
Providing the carrier with an accurate piece count will help to avoid two situations: getting charged a fee and potential pickup issues. Carriers charge a penalty when the shipping papers they receive have errors they need to correct, including the piece count.
If the carrier was expecting a certain piece count for the shipment, a last-minute correction at pickup can cause problems. If they only have space on the trailer for the number of pallets that was originally specified, but it turns out there are more, this will delay the whole shipment process.
How technology helps solve this issue
The answer to avoiding these types of issues is adopting a solution that automatically records the details of the shipment when the items are scanned to be placed with the container, such as the pallet. The chances of errors come from gaps in workflows and redundancy (like retyping information). Technology reduces the opportunity for mistakes as it also improves process efficiency. Similarly, the solution assists with other information on the bill of lading, including the contents of the shipment.
With the right solution, shippers get the benefits of more streamlined workflows in addition to a reduction in errors.
Find out what industry experts from UPS, PARCEL Industry, and TrakMotive have to say about leveraging technology to streamline shipping processes and tackle supply chain challenges by accessing our on-demand Smart Shippers 2022 virtual roundtable recording here.