Blog
Recurring Costs Associated With Legacy Transportation Management Software in Shipping
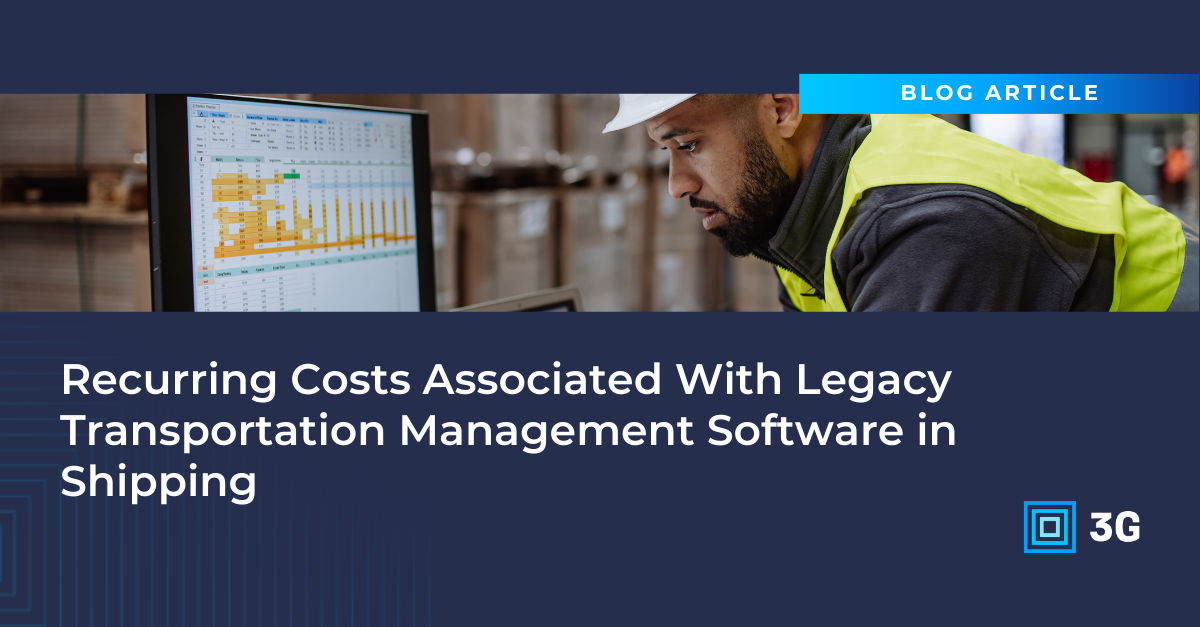
Supply chains are only becoming more complex in terms of scale and the speed with which they move goods. With each passing day, we also see more and more of how limiting it is to use manual systems and track shipments with multiple tools, making it difficult to handle the high volume of shipments necessary to compete in this landscape. This gap in performance is now leading to inefficiencies, a high number of errors, and a lack of real-time visibility into the supply chain.
When you continue to rely on manual systems to manage your shipments, you’re not just slowing down processes and inconveniencing employees — you’re also incurring tangible and unnecessary expenses for your operations, eating into profit margins and long-term success. Digital transportation management solutions are key to breaking through to higher profit margins.
The Cost of Legacy Transportation Management Solutions
Software has evolved to streamline every aspect of transportation management, but many shippers still use paper-based logs, spreadsheets, email chains, and phone calls to get everything done. Even when operations utilize more advanced digital tools, capabilities can be spread out across multiple solutions, creating more manual touchpoints and data silos. These inefficient methods of managing shipments use a variety of techniques and tools, but have one thing in common: They’re time-consuming, labor-intensive, and much more costly than necessary. Using these systems not only hinders your company’s productivity but can also incur additional expenses.
Increased Labor and Administrative Costs
Using spreadsheets and manual paper systems to manage complex shipments, order processing, invoicing, and auditing is incredibly labor-intensive. All the extra time workers spend on basic processes adds up to higher labor and administrative costs. In addition, when shipping routes aren’t planned for maximum efficiency, workers may need to build out and process extra shipments to meet order requirements, potentially increasing shipping costs over time. As automation comes to define the industry more, the legacy methods lacking streamlining capabilities dramatically increase labor budgets.
Higher Shipping Costs
Because manual processes are so time-consuming and cumbersome, they often hinder decision-making and lead to suboptimal planning. Trying to keep track of so much data in different files, it can be easy to overlook the best routes or identify the best carrier rates, leading to missed opportunities for savings. As a result, shippers might select more expensive carriers or inefficient routes, ultimately increasing overall shipping costs for companies.
Excessive Inventory Costs
Across the board, a lack of real-time visibility into inventory levels and efficient routes can cause shippers to hold more inventory than necessary, leading to increased warehousing and other costs. It encourages shippers to maintain higher inventory levels to avoid delays, requiring more storage space to hold the excessive inventory, ultimately increasing storage costs and tying up cash in items they might not need. The inefficient routing associated with legacy systems also leads shippers to build up safety stock to avoid delays in customer orders.
Unnecessary Fuel Spending
In addition to keeping drivers out on the road longer than necessary, poor and inefficient route planning extends mileage, resulting in higher fuel costs. The poor route visibility associated with legacy systems can also make it easy to overlook retailers with better fuel rates, causing drivers to spend more at the pump on top of driving unnecessary miles.
Surprise Fees and Charges
When routes aren’t optimized, drivers are likely to face delays in loading and unloading, resulting in detention fees and other charges from carriers. Drivers must also follow strict regulations about the number of hours they spend on the road before needing a break. Poor route planning can increase the number of layovers they require, potentially incurring additional costs. These unexpected fees add up quickly and can have a substantial impact on transportation budgets.
Higher Risk of Error
Manual spreadsheet and paper log systems create a higher risk of human error in order processing (such as delivery address data and shipping piece counts), or in meeting regulatory compliance standards, such as documenting driver hours of service, emissions data, and vehicle maintenance. Small mistakes can result in costly fines and penalties from regulators. What’s more, compliance mistakes with carrier and partner contracts can jeopardize relationships and even leave shippers open to lawsuits or lost revenue.
Escape Recurring Costs With Transportation Management Solutions
Spreadsheets, paper logs, and other manual transportation management methods may be cheap to implement, but the inefficiencies and errors cost shippers dearly in the long run. And unfortunately, upgrading to multiple digital solutions can leave your workflow just as scattered and cumbersome. What shippers really need is a unified transportation management solution that allows users to implement more automation, consolidate data for reporting, and integrate more effectively with other systems.
A unified platform streamlines route planning, order management, carrier selection, freight payment, and more, allowing users to cut labor costs, reduce shipping fees, avoid accessorial charges, and more. Want to enter a new era of transportation management? Schedule a demo with 3G, today.