Blog
5 Operational Challenges that Impact Transportation Management and How to Meet Them
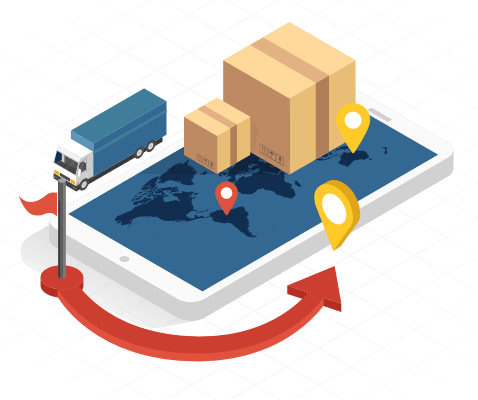
Operational challenges across today’s supply chain are easy to find. Logistics is increasingly complex. Qualified workers are harder to find. And, US trucking freight rates continue to increase, reaching 36% in October 2021—the highest in three decades.
These challenges intensify as the supply chain management market continues to grow. In 2020, the global supply chain management market reached $15.58 billion and is expected to nearly double to $31 billion by 2026.
Between the rising supply chain management market and complexities in logistics, shippers, brokers, and third-party logistics (3PLs) need a simple way to address these challenges. To keep their operations running smoothly, they need a cloud-based transportation management system (TMS). See why a modern TMS makes the ideal tech stack centerpiece for shippers, brokers, and 3PLs to solve today’s complex operational challenges.
What’s next in supply chain organization and operations
As the COVID-19 pandemic plagued nations worldwide, the current supply chain experienced a build-up of its own problems and challenges. Between 2019 and 2021, 68% of supply chain executives responded constantly to high-impact disruptions.
Given the industry-wide need to chart alternative courses during these uncertain times, supply chain organizations started forming partner ecosystems. Through them, over half of large organizations plan to compete as collaborative digital ecosystems by 2026, sharing inputs, assets, and innovations. The benefits of this trend include:
- A more transparent supply chain through shared data
- A better understanding of customer demands
- An improved response to supply and demand changes
Another trend in supply chain operations is the modularity trend. Modularity means turning supply chain resources and processes into discrete blocks of capabilities for quick reuse and reconfiguration. By 2024, supply chains that redesign for modularity will double efficiency by implementing business model innovations over more traditional competitors.
5 operational challenges that impact transportation management
Today’s shippers, brokers, and 3PLs face several operational challenges in managing transportation. Learn more about these challenges, how they affect transportation management, and how you can address them head-on with a TMS.
#1. Cost management errors
The fulfillment process is rife with places where incremental improvements lead to cost savings. Two bottom-line-centric aspects of freight management where these savings apply are route planning and load optimization.
Another area known for errors is carrier freight invoicing. For example, around 20% of invoices for ocean shipments without prepayment audits contain errors. Although error rates for other modes, such as trucking, are lower, error rates for freight invoicing still stand out as a cost management issue. These issues require someone to manually sort through the orders and invoices to find the error, making them inefficient and costly to resolve.
Reduce your operational costs by optimizing freight management functions like route and load management and billing and invoice auditing.
By having a TMS, you address both route and load management issues and carrier freight invoicing errors. Through the combined automation, big data, and analytics, a TMS delivers:
- Route optimization and consolidation. Automated route performance monitoring tracks fleet efficiency. The algorithms recommend carriers use particular order criteria to optimize loads. Each improvement helps save money and boosts efficiency.
- Automated billing and invoice auditing. Catch inaccurate charges and duplicate payments by using the built-in freight payment, consolidation, and auditing services with electronic invoicing. The automated process creates efficiencies by reducing paperwork and removing time-consuming, error-prone manual processes.
- Cost-management advantages. You get the ability to:
- Select the best carrier option.
- Choose the best-suited route.
- Create speed and efficiency across the operation.
- Automate billing and invoice auditing.
#2. Manual operations processes
Operations across transportation management include everything from warehouse, carrier, and freight management to customer service, accounting, and effective use of business intelligence (BI). Optimizing traditional manual operational processes is difficult, if not impossible.
That’s not the case with a TMS. A TMS automates operations through a centralized platform. It provides a single repository for organizational and third-party data. Also, multiple modules address the various operational areas while providing transparency and visibility into the supply chain.
Through a centralized operational platform, optimize operational functions like warehouse management, inventory planning, freight management, payment and freight audits, and customer service.
A TMS provides shippers, brokers, and 3PLs with incremental improvements in every fulfillment function. The key to these optimizations is integrating data, algorithms, and analytics with real-time supply chain visibility and operational decision-making.
In warehouse management, the TMS:
- Works with systems and enterprise resource planning (ERP) software to reduce data entry errors.
- Provides supply chain transparency by improving inventory strategies through better inventory planning and more accurate forecasting.
- Optimizes load and route management through data and analytics that help lower expenses.
A TMS automates payment and freight audits, reducing mistakes and paperwork. It also allows for exception-based management rather than direct oversight over every order detail.
And for customer service, a TMS finds potential problems in real-time and sends alerts to platform users and their customers. This level of support provides transparency in the fulfillment process and builds customer confidence through assurance that order issues are under control.
#3. Lack of visibility
A common factor in meeting cost management and operations challenges is transparency and visibility into the supply chain. For example, shippers don’t have optimal visibility into suppliers’ actions, which affects overall transportation efficiency. The lack of visibility creates breakdowns in transportation management and affects the ability to optimize inventory across the supply chain.
Get end-to-end fulfillment visibility into order tracking and transparency for vital status information. Use the collected data in the TMS to improve operations and inventory efficiency.
Traditional manual operational processes don’t provide the level of transparency that today’s supply chain demands. By using a TMS as a centralized software platform in the transportation technology stack, you remove many barriers to transparency and dramatically improve visibility.
With end-to-end fulfillment visibility, a TMS enables you to:
- Track orders, from origination through delivery. Get information about deliveries and delays, increasing user and customer confidence in on-time delivery.
- Manage service disruptions. When a service disruption occurs, the TMS creates real-time alerts that allow for immediate adjustments to streamline operations and improve customer service.
- Collect valuable data. Get order details and performance metrics like on-time delivery. The TMS feeds this data into analytics and reporting to improve operations.
- Increase inventory efficiency. Take advantage of better planning and more accurate forecasting.
#4. Delivery issues
Successful on-time delivery is the goal of every order. The critical elements to ensure delivery include supplier oversight and the ability to execute vendor shipments. However, a lack of visibility creates issues in aligning order fulfillment with business demands. And not having the ability to coordinate those needs in transportation management impacts delivery.
Improve delivery by getting real-time order alerts to help transportation managers find and fix delivery issues and provide customers with immediate updates on order status.
A TMS provides the fulfillment visibility and automated capabilities to optimize deliveries in the following ways:
- Carrier management. A TMS streamlines everything from carrier qualification and onboarding to carrier assignment, shipment execution, and status tracking.
- Order pricing. A TMS provides data-driven algorithms to improve and optimize order pricing.
- Operational processes. Route and load management improve order execution. Fleet tracking provides data to further improve future deliveries.
- Real-time alerts. A TMS issues automated real-time alerts on deliveries and delays. Immediately upon discovery of a problem, the platform alerts users, providing the order information to solve it and suggesting potential solutions to help transportation managers fix fulfillment issues.
For customers, order visibility means they also know details about every order, including delivery delays and fulfillment issues. The result is increased confidence in the shipper, broker, or 3PL and improved customer satisfaction with the service provided.
#5. Ineffective business intelligence
Accurate, timely, and relevant data are the lifeblood of BI. However, the data and information in traditional manual transportation management processes are difficult to collect and collate into usable formats.
Also, technology alone isn’t an effective solution to the BI challenge. BI requires organization-wide analytical and reporting oversight. But decentralized data repositories and a technology stack of siloed software solutions that address specific transportation management functions make that oversight impossible.
Through a central repository of organizational data, give users access to analytics and reporting tools through user-friendly dashboards.
A TMS serves as a centralized data repository. It consolidates data from diverse internal and external systems and sources across inventory databases, vendor databases, and fulfillment systems. This data storehouse powers the algorithms behind operational optimizations and provides the raw material for BI analytics and reporting.
TMS dashboards help users turn analytics and reports into actionable strategies. For example, they can find areas for cost savings, identify new business opportunities, and uncover ways to increase profitability and improve operational efficiency.
Meet transportation management challenges head-on
The operational challenges of transportation management described in this post weigh heavily on shippers, brokers, and 3PLs, costing both extensive time and valuable money. Meet these challenges with a modern, cloud-based TMS platform.
A TMS helps transportation management companies grow and keep pace with trends, like partner ecosystems and modularity. It delivers value by streamlining daily operations and creating efficiencies across the organization.
The platform fits seamlessly into the transportation management tech stack and maintains a central repository of internal and external data. This single platform provides automation across operational functions and helps optimize fulfillment processes.
See how a TMS helps solve transportation management challenges with carrier capacity. Read our post: Looking for carrier capacity? Look for a Transportation Management System.